Transforming raw materials into yarns and fabric, the textile industry weaves a world of diverse products for fashion, home, and industrial applications.
Solutions for
Textile
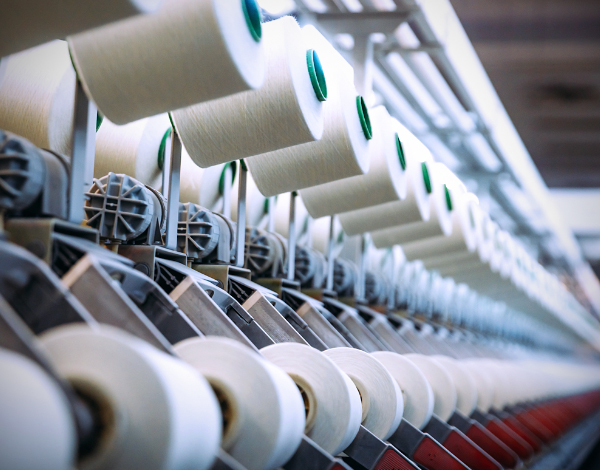
OVERVIEW
Textile manufacturing begins with the conversion of fiber into yarn, then yarn into fabric. These are then dyed or printed, fabricated into clothing. Cotton, wool, silk, and a variety of bast fibers (hemp, flax, and jute) undergo several mechanical operations in preparation for several available finishing processes which are typically chemical in nature. In addition to chemical finishing, synthetic fibers are produced using an extrusion process. Extrusion, as well as all chemical finishing processes utilize chemical treatment tanks and piping which benefit from the over-pressure protection provided by ZOOK rupture disks.
COMMON APPLICATIONS
Bulk Storage Tanks
A chemical reactor is an enclosed volume in which a chemical reaction takes place and is generally understood to be a process vessel used to carry out a chemical reaction. Whether a batch or continuous reactor vessel, chemical reactions often result in the release of gases or the generation of heat, which in either situation, increase internal vessel pressure. To insure the integrity of the vessel, connected piping, valves and process instrumentation, rupture disks provide safe release of excess pressure.
Bleaching
Bleaching improves whiteness by removing natural coloration and remaining trace impurities by adding an oxidizing agent, typically hypochlorite or peroxide.
Safety Relief Valve Isolation
A safety relief valve automatically releases pressure from a boiler, pressure vessel, or other system, when the pressure or temperature exceeds preset limits. A rupture disk is an excellent solution for isolating the pressure relief valve from a chemical process when the process fluid is highly corrosive to the relief valve’s internal components. In addition, using a rupture disk in combination with a relief valve, extends the life of the safety valve.
Scouring
Scouring, is a chemical washing process carried out on cotton fabric to remove natural wax and takes place in closed heated iron boilers, called kiers, which washes the fibers with sodium hydroxide under pressure.
Synthetic Fiber Extrusion
Most synthetic and cellulosic manufactured fibers (acrylic, nylon, rayon, polyester, spandex) are created by “extrusion” — forcing a thick, viscous liquid through the tiny holes of a device called a spinneret to form continuous filaments of semi-solid polymer. The pressure required for extrusion is high and rupture disks from ZOOK protect the extrusion equipment against over-pressurization
Boiler and Boiler Feed Piping
Textile processing and conditioning vessels are heated using steam and hot water. In the event of an over-pressure condition, ZOOK rupture disks are designed to activate providing relief of excess pressure before damage can occur to boilers and connected piping.
PRODUCTS BY APPLICATIONS
There are many other pressure relief applications we provide to the Textile. Please contact ZOOK for applications not listed.
Recommended Products | Bulk Storage Tanks | Scouring | Bleaching | Synthetic Fiber Extrusion | Boiler & Boiler Feed Piping |
---|---|---|---|---|---|
Engineered to Order
|
|||||
Graphite Disks
|
|||||
Ultra-Low & Bi-Directional Disks
|
|||||
Plugs
|
|||||
Holders
|
|||||
Holders
|
|||||
Accessories
|
|||||
Explosion Vents
|
Applications List
Bulk Storage Tanks
Recommended Products
Graphite Disks
Ultra-Low & Bi-Directional Disks
Holders
Holders
Accessories
Explosion Vents
Scouring
Recommended Products
Graphite Disks
Ultra-Low & Bi-Directional Disks
Holders
Holders
Accessories
Bleaching
Recommended Products
Graphite Disks
Ultra-Low & Bi-Directional Disks
Accessories
Synthetic Fiber Extrusion
Recommended Products
Boiler & Boiler Feed Piping
Recommended Products
Graphite Disks
Holders
Holders
Accessories