Through complex reaction and refinement processes, the chemical processing industry converts raw materials into various chemicals and products.
Solutions for
Chemical Processing
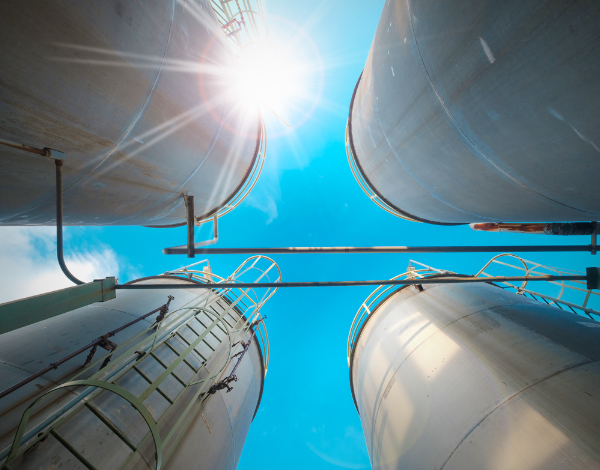
OVERVIEW
Safety is of primary concern in Chemical Processing Industries as many of the process liquids and gasses used can produce a variety of unsafe conditions. Over-pressurization of reactor and process containment vessels, as well as fluid transfer piping is a potential hazard that can result in catastrophic results to the process, the environment, and plant personnel.
COMMON APPLICATIONS
Reactors & Process Vessels
A chemical reactor is an enclosed volume in which a chemical reaction takes place and is generally understood to be a process vessel used to carry out a chemical reaction. Whether a batch or continuous reactor vessel, chemical reactions often result in the release of gases or the generation of heat, which in either situation, increase internal vessel pressure. To ensure the integrity of the vessel, connected piping, valves and process instrumentation, rupture disks provide safe release of excess pressure.
Heat Exchangers
Heat exchangers are used to transfer heat between solid object and a fluid or from one fluid to another. The fluids, liquids or gas are typically separated by a solid wall to prevent mixing. Used in a broad range of industries including chemical, power generation, refining and waste treatment, the safety concerns regarding over-pressurization heat exchangers, steam jacketed vessels and piping, just to name a few, are addressed using rupture disks.
Safety Relief Valve Isolation
A safety relief valve automatically releases pressure from a boiler, pressure vessel or other pressure system when the pressure exceeds pre-set limits. A rupture disk is an excellent solution for isolating the pressure relief valve from a chemical process when the process fluid is highly corrosive to the safety relief valves internal components (trim). By installing a rupture disk fabricated from special alloy rather than the valve trim will dramatically reduce the cost of the safety relief valve. In addition, using a rupture disk in combination with a safety relief valve provides zero process leakage, the release of fugitive emissions and allows in-situ testing of the safety relief valve and extends the working life of the safety relief valve.
Chillers
A Chiller is a machine that removes heat from a liquid via a vapor-compression or absorption refrigeration cycle. This liquid can then be circulated through a heat exchanger to cool equipment, or another process stream. There are several methods used to compress the refrigerant gas during the vapor-compression cycle. Rupture disks provide protection against over pressurization.
Bulk Storage Tanks
Storage tanks containing raw materials, as well as finished processed chemical products require protection against over-pressurization. Liquid, gas and dry chemicals can be flammable, corrosive, and extremely hazardous to people and the environment are stored and transported in compressed form in pressurized containers under high pressure. Dry products, such as fertilizers, processed grains, and thermoplastic beads stored in silos, can produce explosive dust, for which vent panels are used to help relieve excessive forces.
PRODUCTS BY APPLICATIONS
There are many other pressure relief applications we provide to the Chemical Processing Industry. Please contact ZOOK for applications not listed.
Recommended Products | Reactors & Process Vessels | Chillers | Heat Exchangers | Bulk Storage Tanks | Safety Relief Valve Isolations |
---|---|---|---|---|---|
Graphite Disks
|
|||||
Ultra-Low & Bi-Directional Disks
|
|||||
Holders
|
|||||
Holders
|
|||||
Accessories
|
|||||
Explosion Vents
|
Applications List
Reactors & Process Vessels
Recommended Products
Graphite Disks
Holders
Holders
Accessories
Chillers
Recommended Products
Graphite Disks
Holders
Holders
Accessories
Heat Exchangers
Recommended Products
Graphite Disks
Holders
Holders
Accessories
Bulk Storage Tanks
Recommended Products
Graphite Disks
Ultra-Low & Bi-Directional Disks
Holders
Accessories
Explosion Vents
Safety Relief Valve Isolations
Recommended Products
Holders
Holders
Accessories