Metal Rupture Disks are made from very thin materials that have been carefully selected by actual trial and not by calculation. As a result, the strength is exactly what is required and there is no ‘corrosion allowance’ or other safety factors. The service life of the disk depends on many factors which could cause the disk to burst prematurely, some of these being:
Operating Pressure
All rupture disks have what is called an Operating Ratio (specified OR percentage is used to calculate the maximum operating pressure, see disk data sheet for more information) This varies for different disk designs and can be from 50% – 95%. To illustrate this, if the rupture disk has a 90% operating ratio and is rated at 145 psig (10 barg) with a +/- 10 % burst tolerance, to achieve a good service life the rupture disk should not be subjected to a system operating pressure in excess of 90% of the rupture disk’s minimum rated burst pressure (i.e. 145 psig (10 barg) less 10% burst tolerance multiplied by 90% = 117.5 psig (8.1 barg). If the rupture disk encounters pressures above this, it could stress the rupture disk membrane causing fatigue of the metal or graphite and could result in premature failure.
A rupture disk can become fatigued in pulsating type conditions. Some rupture disk designs are better suited than others for this type of duty i.e., ‘Reverse Acting’ (Reverse Buckling) type rupture disks.
Temperature
The temperature can affect the burst pressure of the rupture disk. For example, if the rupture disk is ordered at a particular pressure and temperature any temperature variance in the process conditions will affect the burst pressure of the rupture disk. It will be progressively weaker as the temperature rises and progressively stronger as the temperature decreases. The effect will vary depending on the rupture disk design and material of construction.
Pressure Cycling
Pressure cycling refers to the repeated rise and fall of pressure within a system, which can have a significant impact on the service life of a rupture disk. This cycling includes both gradual changes in pressure as well as more rapid fluctuations, commonly referred to as pulsating. While pulsating is a form of pressure cycling characterized by high-frequency, low-amplitude variations, pressure cycling as a whole encompasses a broader range of pressure changes. Both forms of pressure cycling can lead to material fatigue in the rupture disk, potentially reducing its burst pressure over time and increasing the risk of premature activation or failure. Some rupture disk designs are better suited than others for this type of duty e.g. Reverse Acting (Reverse Buckling) type rupture disks. Understanding and managing the specific type of pressure cycling, including pulsating, is crucial for maintaining the rupture disk’s performance and extending its service life.
Corrosion Condition
It is important that the material of construction of the rupture disk is checked to be compatible with the service duty. Any corrosion of the rupture disk membrane will affect the burst pressure of the rupture disk. A rupture disk can be made from various materials, such as, 316SS, Nickel, Inconel, Monel, Aluminum, Hastelloy-C276, Tantalum, and Graphite etc.
Uneven or Over Torque of the Rupture Disk Assembly
Not all rupture disk assemblies are non-torque sensitive. Applying an incorrect torque on the assembly can result in the rupture disk not bursting within the rupture disks specified burst range and/or cause damage to the rupture disk.
Orientation of the Rupture Disk Assembly
It is very important that the rupture disk and holder assembly are installed in the correct flow direction. If the rupture disk or the complete assembly is installed in the incorrect flow direction, the rupture disk now could be many times stronger than the rated burst pressure stamped on the rupture disk tag. ⚠️The results of the rupture disk not bursting when required could be catastrophic. There are ‘FLOW ARROWS’ on both the rupture disk tag and the holder tag showing the direction of the flow to assist with the correct orientation of the rupture disk and holder assembly.
Handling and Storage
It is very important that the rupture disks are stored and handled correctly. The membranes of the rupture disks are very delicate. Any damage to the dome or seat of the rupture disk while storing, handling, or installing the rupture disk will affect the burst pressure. Many rupture disk designs are designed to be ‘fail safe’ and will burst at a lower pressure than rated if the dome is damaged. Also, some single membrane design rupture disks, which are made to withstand full vacuum conditions, will fail under vacuum conditions if the membrane/dome of the rupture disk is damaged in transit or installation.
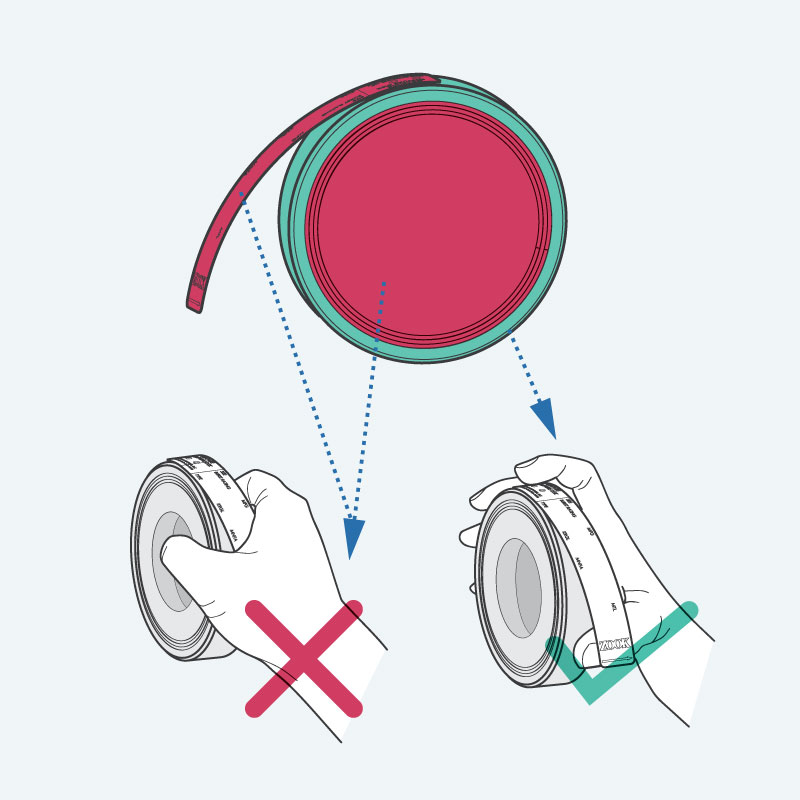
Proper Handling of a Graphite Rupture Disk

Proper Handling of a Metal Rupture Disk
Downstream Conditions
Downstream conditions, for example, back pressure, condensation or debris can also affect rupture disk performance.
The cost of replacing a rupture disk that has burst prematurely can be very high, particularly if the system must be shut down to replace the rupture disk. Accordingly, we recommend all rupture disks be replaced periodically even if they appear to be in good condition. A convenient time to do this would be when the system is shut down for planned maintenance.
For more information on rupture disk change-out frequency, contact us today.
Originally published June 2021, updated August 2024.