RUPTURE DISKS AND SAFETY VALVES HAVE THEIR OWN STRENGTHS AND WEAKNESSES. HOWEVER, USING A RUPTURE DISK WITH A SAFETY VALVE WILL ELIMINATE IMPORTANT OPERATIONAL CONCERNS AND PROVIDE BOTH CAPITAL AND MAINTENANCE COST SAVINGS.
ABSOLUTE LEAK-TIGHTNESS
A spring loaded, metal to metal safety relief valve begins to leak the closer to the operating pressure it approaches. This is called “simmer” and is part of the valve design. A rupture disk positioned upstream of the safety valve ensures a leak-tight seal, eliminating the leaking during the simmer.
The valve will also tend to leak if used in a corrosive environment, which will eventually damage the sealing surface of the valve. To solve this problem, a rupture disk used with a safety valve will protect the valve by creating a barrier between the valve and the process.
In addition, fugitive emissions are an ongoing concern and in many countries there are regulations in place for the monitoring of these gas emissions. Adding a rupture disk with a safety valve provides a superior process seal reducing fugitive emissions.
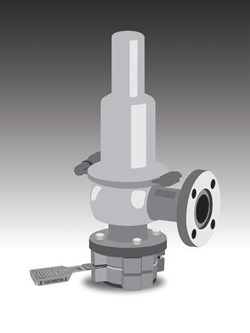
SAFETY VALVE TESTING
Using a rupture disk with a safety valve will allow you to perform on-site testing without removing the valve. Some companies still require the removal of the safety valve for off-site testing and servicing. The cost of adding a rupture disk is much less expensive than the loss of production time that will occur when removing or re-assembling the safety valve.
EXTENDING THE LIFE OF THE SAFETY VALVE
The rupture disk acts as a barrier protecting the safety valve against corrosion and protection of the process. It also protects against operating conditions which affect the function of the safety valve. All of these factors will protect the safety valve from a corrosive environment and extend the life of the safety valve. It’s also worth noting that it’s much less expensive to replace a rupture disk than a safety valve.
REDUCING COSTS OF SAFETY VALVE MATERIALS
Safety valves used in a corrosive environment require to be lined or made from expensive materials that are resistant to corrosion.
If a safety valve is combined with a rupture disk, it would be the rupture disk that would be in contact with the medium and would need to be made from anticorrosive material. This would substantially reduce costs, as a safety valve with the wetted parts made from exotic alloys is much more expensive than a rupture disk made from exotic alloys.
There are many benefits in using a rupture disk with a safety valve, such as increased safety, decreased costs, and improved plant operations performance.