The demands on plastic extrusion machines have become more challenging over the past years, due to increased production
demands, and the desire to extend the operational life of equipment. These two ongoing factors tend to result in excessive build-up of pressure in an extrusion machine which can lead to major machine malfunction, costly downtime and operator safety issues.
WHEN LOOKING FOR AN EXTRUSION BURST PLUG TO PROTECT YOUR PLASTIC EXTRUSION MACHINE ALWAYS ASK FOR THESE 4 PRODUCT FEATURES:
1. WELDED NOT SOLDERED CONSTRUCTION
Traditionally the thin rupture disk membrane is attached to the threaded body using a soldering process which can fatigue in cycling applications and loses strength and burst consistency as temperatures increase to the planned extrusion temperature all of which lead to reduced service life, costly downtime, unforeseen maintenance, and in extreme cases damage to the extruder machine itself. Today, modern welding technology eliminates all of these worries ensuring the highest quality longest lasting extrusion burst plugs that are repeatable, predictable, and the joint is unaffected by the varying temperatures of the extrusion process. In addition, welded construction offers flush mounting of the extrusion burst plug reducing the potential of product build-up common in a soldered joint.
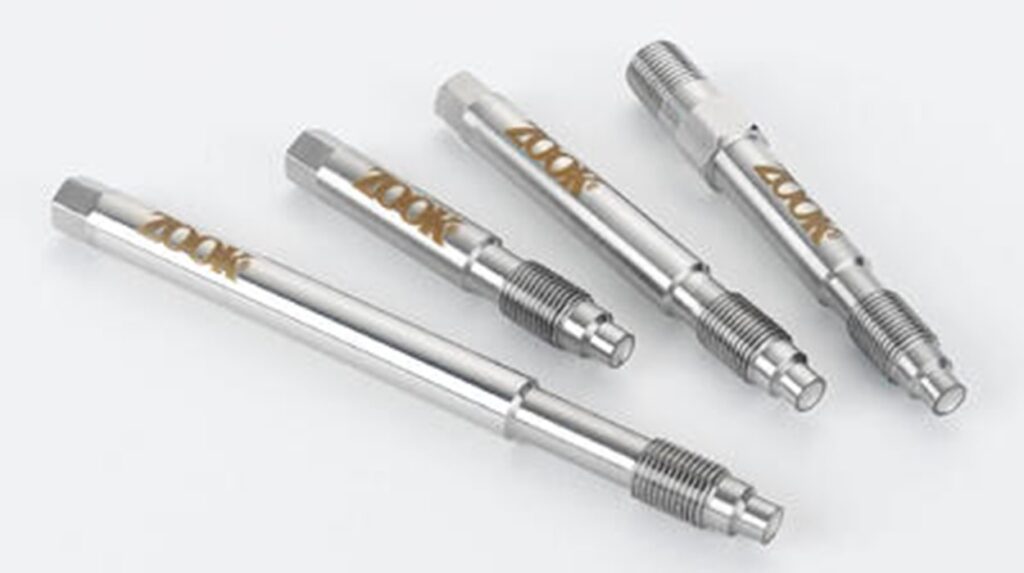
2. FULL TRACEABILITY
A pressure relief device is designed to protect capital equipment and plant personnel and therefore needs to be made by a manufacturer experienced in the pressure relief field from certified materials in accordance with recognised global standards.
Always ask who, where, and what recognized standards are being followed to guarantee the highest quality pressure relief device. This should be supported by certified material test certificates issued by the mill and burst and leak test certificates issued by the device manufacturer.
3. FINAL PRODUCT TESTING
When a completed batch of extrusion burst plugs are produced a series of final acceptance tests are mandatory in order to qualify the finished product. Destructive testing of a suitable quantity of finished product to meet international standards is a must to ensure compliance to industry standards. Leak testing should be performed to avoid costly downtime and to ensure that the extrusion burst plug joint is perfect on each completed unit.
Inspection of different thread types can be subjective when it comes to traditional methods utilizing ring and plug gauges. By undertaking 100% electronic thread verification with an optical comparator each thread on the device is compared to the international standard to ensure the pitch, roundness, taper etc., is perfect and will install correctly without the fear of damaging the female threads within the plastic extrusion machine.
4. DOCUMENTATION AND MARKING
Always insist on receiving proper documentation that details the destructive and non-destructive test results performed during manufacture. Also, insist that such destructive and non-destructive tests are undertaken to known international standards such as ISO 4126-2/PED.
Insist that the device be permanently marked in accordance with the specified standard including the manufacturers’ lot number, burst pressure and temperature, and manufacturers’ name.
Safety is of paramount importance and should never be compromised by cost cutting on unknown materials of construction, outdated manufacturing procedures or lack of material and performance certification.